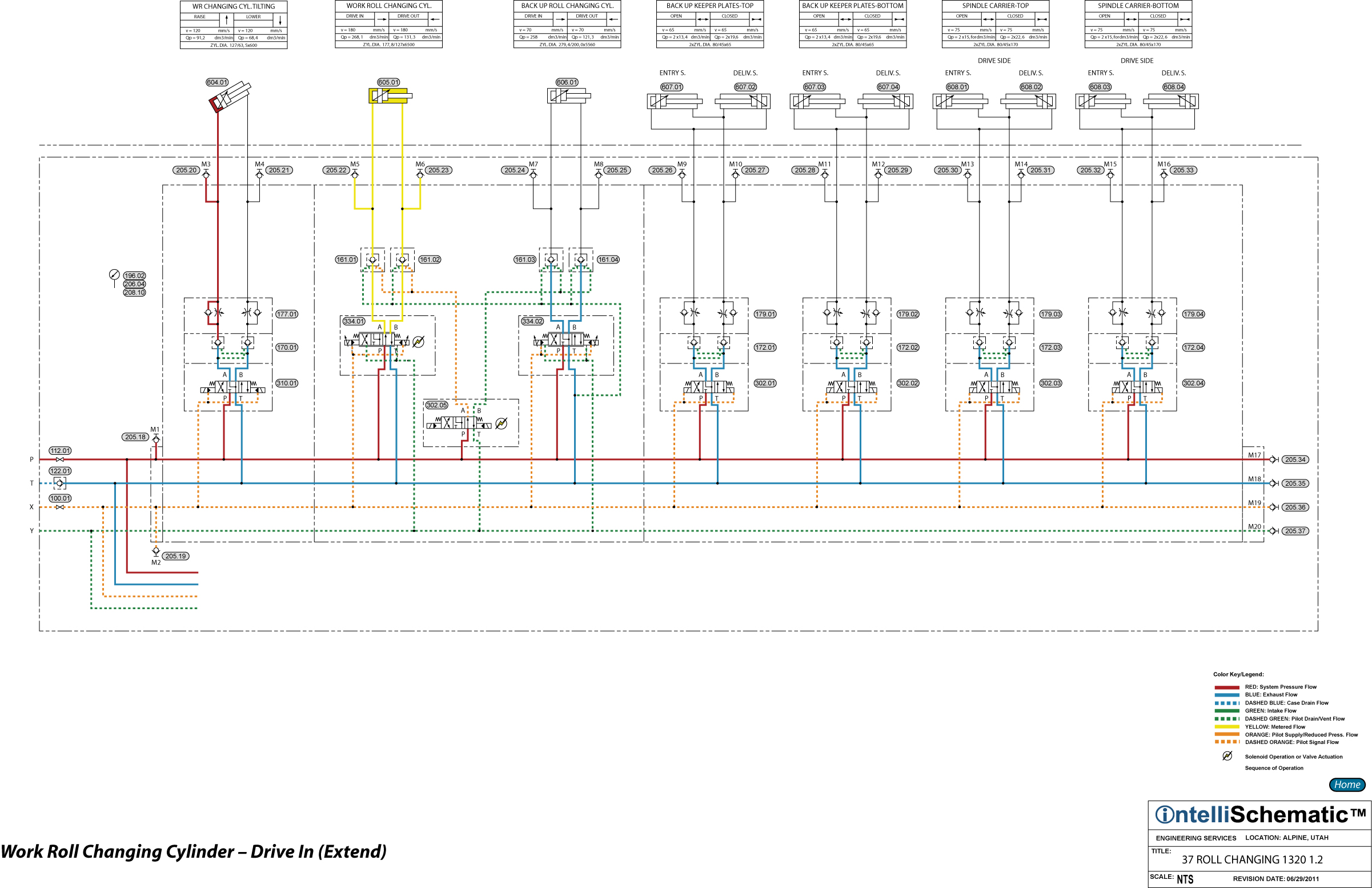
![]() ![]() ![]() ![]() ![]() |
Work Roll Changing Cylinder - Drive In (Extend) |
For previous sequences in this event see the event “Roll Change HPU – On.”
Note that this event describes the sequences for Mill Stand F1. The same sequences apply for stand F2 through F6, though the component numbers will change. Refer to the relevant schematic for each stand for the appropriate component number.
1) Directional Control Valve 302.05 is energized to the parallel flow pattern allowing pressurized hydraulic fluid to flow through the valve passing from P to A. This fluid then flows to the pilot ports of Pilot Operated Check Valves161.01 and 161.02, piloting these valves open. At the same time, the pilot pressure ports of Pilot Operated Check Valves 161.03 and 161.04 are vented, ensuring these two check valves remain closed, thus preventing Backup Roll Changing Cylinder 606.01 from being moved, even if Proportional Directional Control Valve 334.02 is energized in either direction.
2) Proportional Directional Control Valve 334.01 is energized to the parallel flow pattern allowing pressurized hydraulic fluid to flow through the valve passing from P to A. The fluid then flows freely through Pilot Operated Check Valve 161.01, then into the cap end of Work Roll Changing Cylinder 605.01, causing the cylinder to extend. Note that the proportional directional control valve achieves speed control of the extension rate of the cylinder using both meter-in and meter-out flow control.
3) Exhaust fluid from the rod end of the cylinder flows freely through Pilot Operated Check Valve 161.02, which has been piloted open by pilot pressure from the A-side of the circuit.
4) Finally, the exhaust fluid flows back to tank through Proportional Directional Control Valve 334.01, passing from B to T, Check Valve 122.01 and Duplex Return Line Filter 045.01.