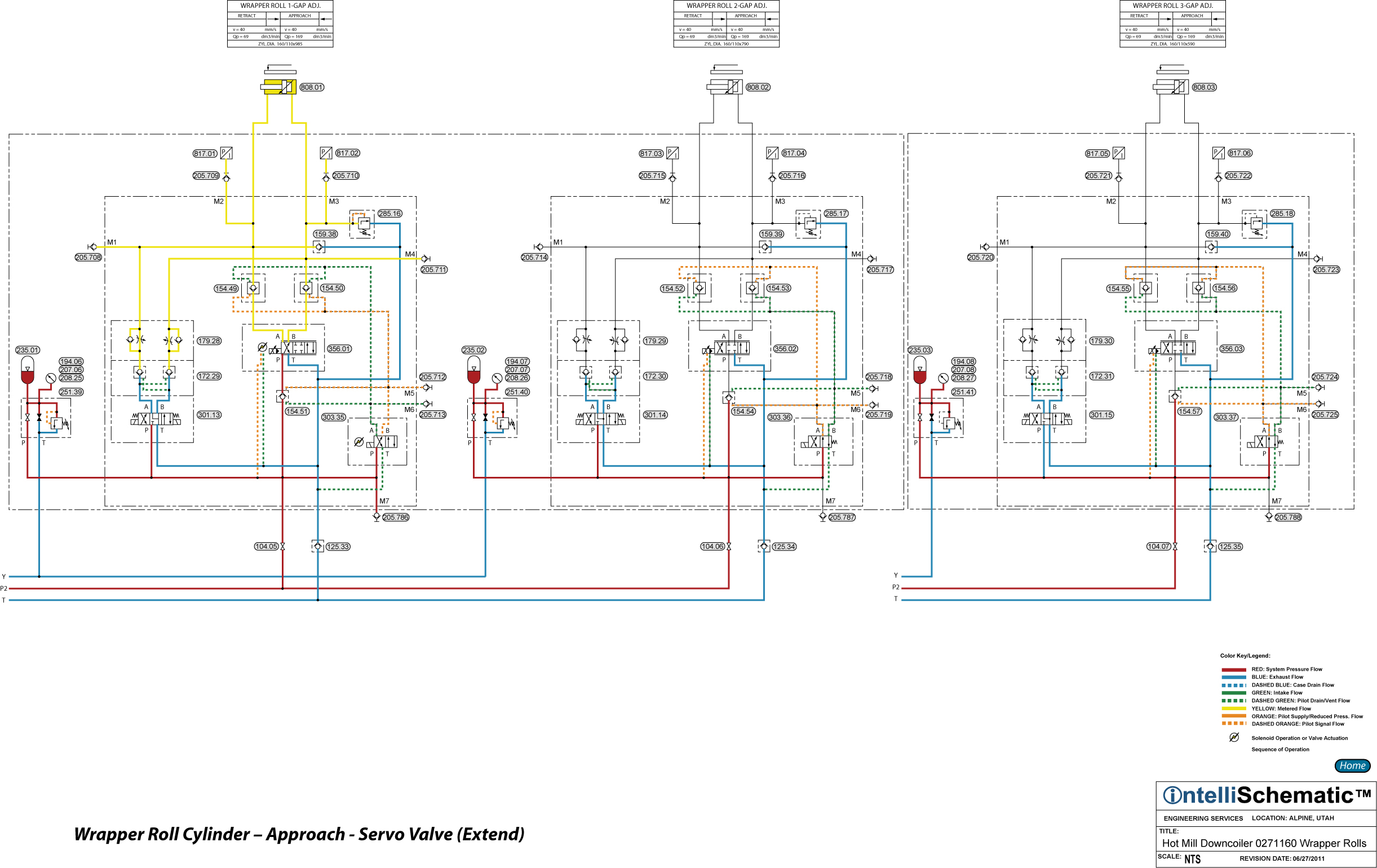
![]() ![]() ![]() ![]() ![]() |
Wrapper Roll Cylinder - Approach - Servo Valve (Extend) |
For previous steps in this sequence see the event “HPU – On.”
1) Directional Control Valve 303.35 is energized to the crossover flow pattern allowing pressurized fluid to flow through the valve, passing from P to B. This fluid flows to the X-ports (pilot pressure ports) of Pilot Operated Check Valves 154.49, 154.50 and 154.51 piloting these valves open. Simultaneously the Y-ports (pilot drain ports) of the pilot operated check valves are vented through the directional control valve, as port A is connected to port T. As a result, pressurized fluid may flow to the P-port of Servo Valve 356.01 and the cylinder ports of the valve (the A & B ports) are connected to Wrapper Roll 1-Gap Adjustment Cylinder 808.01.
2) Servo Valve 356.01 is energized to the crossover flow pattern and pressurized hydraulic fluid flows through the valve passing from P to B. The fluid then flows freely through Pilot Operated Check Valve 154.50 into the cap end of the cylinder causing the cylinder to extend.
3) Exhaust fluid flows from the rod end of the cylinder, through Pilot Operated Check Valve 154.49 (which was piloted open in step 1, above), through the servo valve, passing from A to T, then back to tank through Check valve 125.33 and Duplex Return Line Filter 045.03.
4) Note that the retraction speed and position of the cylinder is controlled by the servo valve.
5) Note that Accumulator 235.01 provides instantaneous flow for the servo valve and Pressure Relief Valve 285.16 protects the cap end of the cylinder from overpressure. Pressure Relief Valve 285.16 protects the cap end of the cylinder from overpressure caused by load forces and Check Valve 159.38 provides make-up fluid to prevent cavitation at the rod end of the cylinder during the forced retraction of the cylinder.